HEULE COFA Deburring Tool Featured in Production Machining
Swiss Precision Since 1961
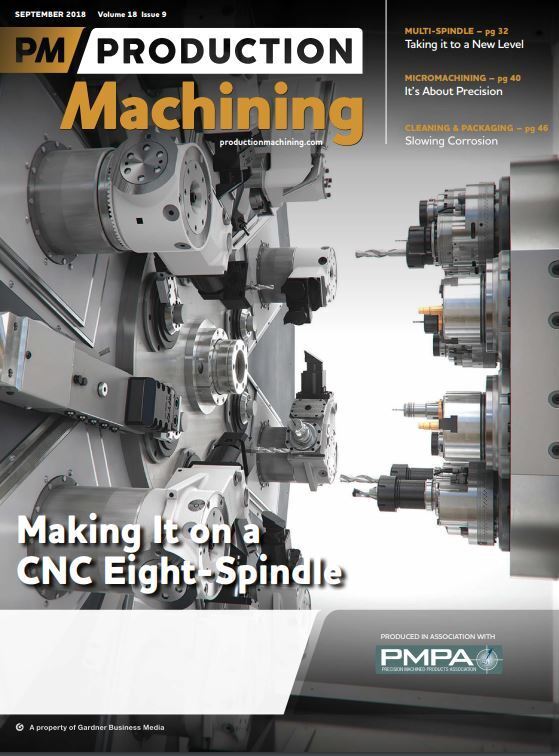
Automated Deburring Tool Increases Production of Subsea Valves
Multiple difficult-to-reach holes, each of varying sizes, and of varying quantity depending on the part in question made machining subsea valves at Abco Subsea difficult. But ever since the company found the Cofa C Series tooling from Heule Tool, it has worked flawlessly in the production line.
More than 30 years ago, Abco Subsea (Houston, Texas) patented the first multi-input shuttle valve, a product that is now installed on more than 20 percent of the world’s deepwater drilling fleet. Subsea products must withstand a lifetime of corrosion under the ocean without breaking down. Abco has become one of the largest providers of BOP shuttle valves to the offshore industry with a product that is meticulously manufactured, according to the company, even with increasing demand and production targets.
Producing a product with a lifetime guarantee is no small feat for Jerry Cross, CNC manufacturing manager at Abco Subsea. In 2015, Abco brought production of the hydraulic shuttle valves in house to increase quality and consistency. Originally made of aluminum bronze, the company wanted a new line of valves made of nitronic. Mr. Cross was the point person for setting up a machine shop that would eventually manufacture 2,000 parts a month.
Multiple difficult-to-reach holes, each of varying sizes, and of varying quantity depending on the part in question made machining difficult, even for Mr. Cross and his expert team of CNC operators. Drilling happens all in one operation on a lathe by indexing the part with the C axis at 90 degrees and using an end mill to drill the hole.
Mr. Cross tried a ceramic deburring tool, which broke apart and sent pieces flying everywhere. He tried having his team deburr manually with a router or die grinder, or using sandpaper, which left his operators worn out and didn’t necessarily guarantee a perfectly deburred chamfer.
With quotas that vary from 700-2,500 holes per month, Mr. Cross needed a solution that would get the job done and grind down the part—not his employees.