Aerospace
Swiss Precision Since 1961
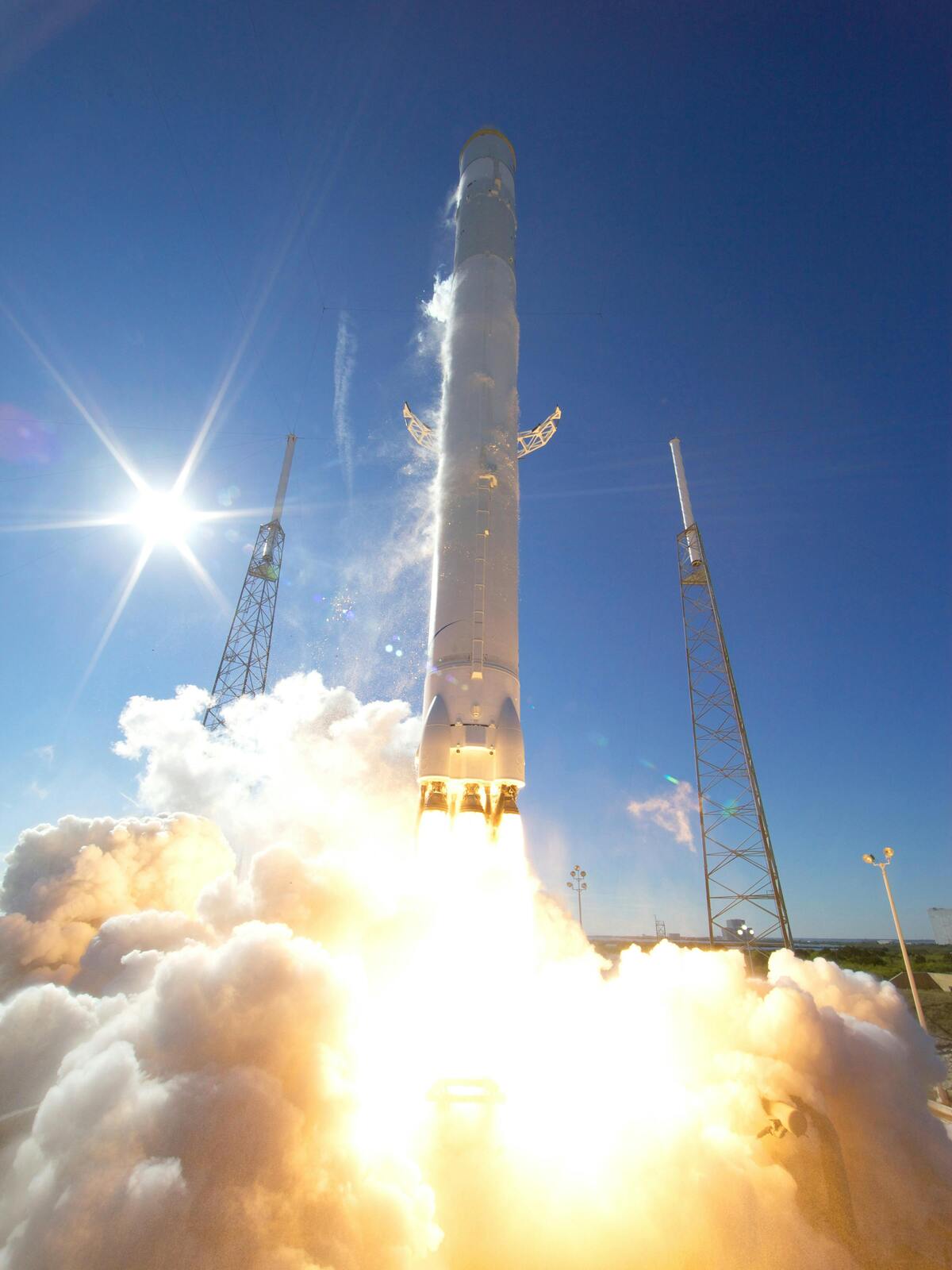
Precision Cutting Tools for Aerospace Manufacturing
In the aerospace industry, where precision and efficiency govern production, even the minutest details can significantly influence the overall quality and cost-effectiveness of manufacturing.
At HEULE, we collaborate closely with manufacturing engineers to develop cutting tools that streamline operations, enhance process optimization, and deliver superior quality components.
Our aim is to ensure that these small details make a substantial impact on your bottom line and the quality of your aerospace projects.
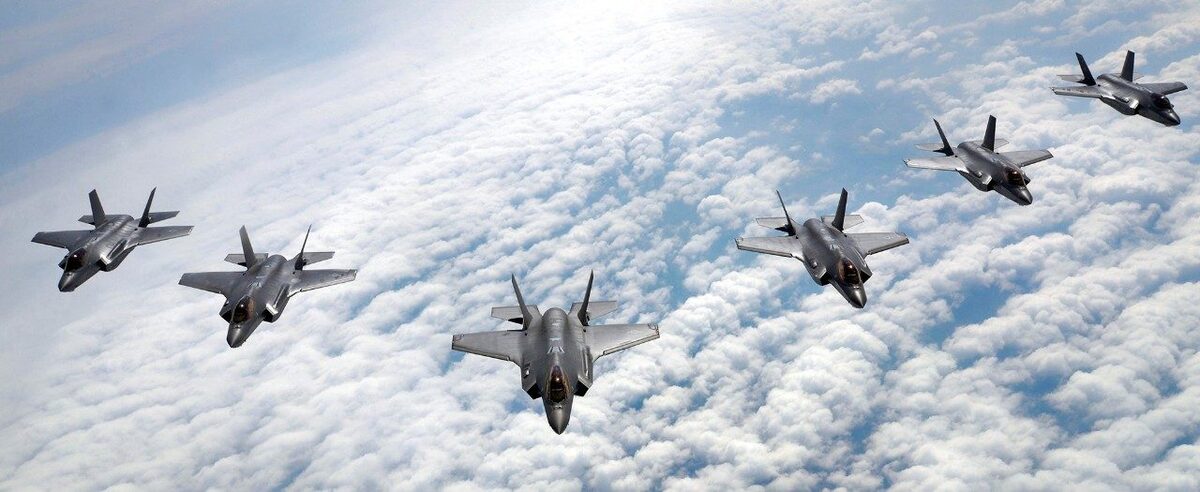
Key HEULE Tools for Aerospace Applications
- DEFA (Adjustable Chamfering) - Tailor your chamfering requirements with precision to meet diverse aerospace specifications.
- COFA (Universal Deburring) - Achieve smooth, flawless finishes on a variety of materials, crucial for aerospace component integrity.
- BSF (Large Ratio Spotfacing) - Perfect for creating precise counterbores on critical aerospace parts where back clearance is limited.
- SOLO (Powerful Automatic Front & Back Boring) - Engineered for high-performance, ensuring reliability and accuracy in critical boring operations.
- COMP (Combination Countersinking & Drilling) - Streamline multiple drilling and countersinking processes into a single step, enhancing efficiency and reducing tool changeover time.
Each tool is designed with a focus on innovation, reliability, and quality to meet the rigorous standards of the aerospace industry. Explore our solutions to see how HEULE can elevate the efficiency and quality of your aerospace manufacturing processes. If you have questions or need expert advice on the right tools for your projects, don't hesitate to contact our team. We’re here to help you achieve the best results.
"The BSF tool performed so well that I have now cut out the other five axis roughing, saving us three operations in total and 15 minutes in cycle time."