Case Studies
Showing Entries for 2017
Entry Tags (33 found)
Aerospace Aluminum Automotive Back Counterboring Brass BSF Cast Iron Chamfering Cobalt-Chromium Alloy COFA COFA-X Composite Counterboring Countersinking Cross Hole Deburring Deburring DEFA Drilling Energy GH/E Heavy Equipment Inconel Medical Nickel Polyether Ketone (PEEK) Precision Machining SNAP SOLO Spotfacing Steel VEX-P VEX-S X-Bores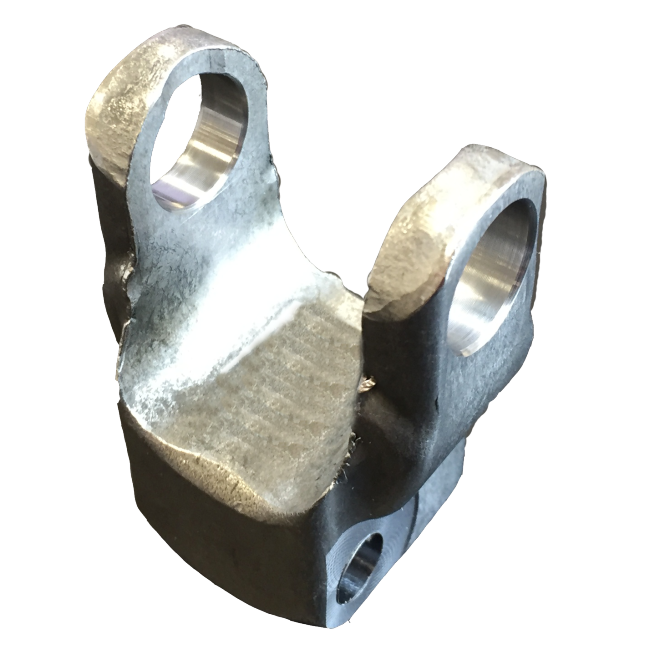
A subcontractor to the automotive industry used to deburr a fork laboriously by hand. The fork is part of the steering column. Faced with the problem that the manual deburring was too time-consuming a...
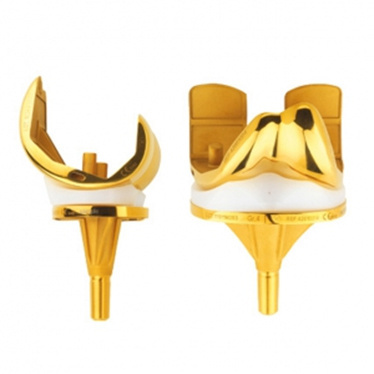
An artificial joint manufacturer in the medical technology field was not happy with the existing manual deburring solution of a crossbore in a knee replacement part and the quality of the parts being ...
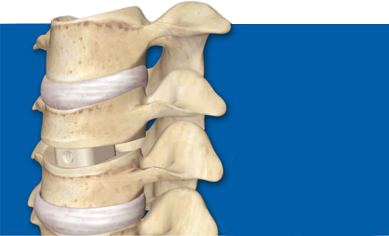
The customer was looking for a solution to deburr/chamfer bores of back implants for the medical industry. The material, PEEK (Polyether ketone), posesses a very high continuous service temperature, s...
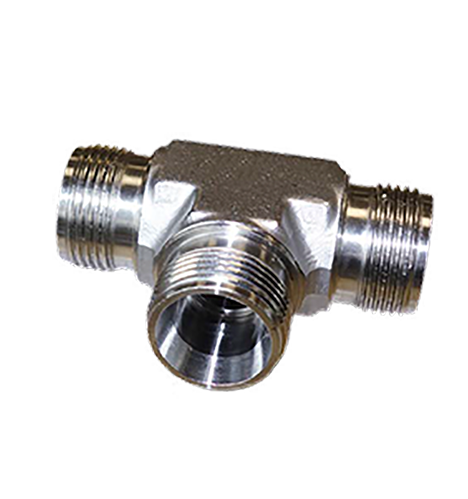
A manufacturer of hydraulic components and fittings was looking for a more efficient and safer deburring solution for the cross hole of a ball valve. The goal was to automate the process and eliminate...
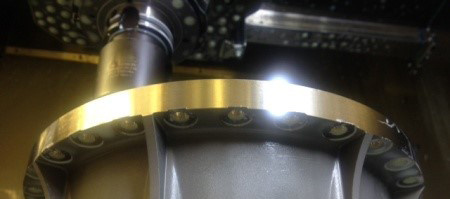
An aerospace manufacturer was machining 30 back spot facings in a component made of Inconel 718 for some years. To do this, the part needed to be set up several times because of the poor accessability...
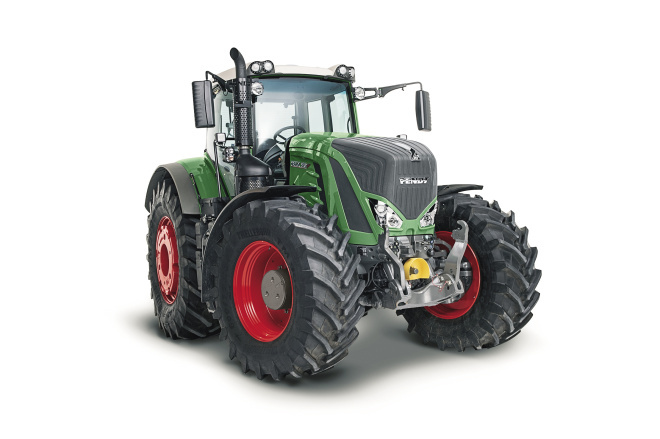
Countersinking Bores for a Tractor Component
A major heavy equipment manufacturer was looking for a solution to produce countersinks on bores for a gear component on a tractor.
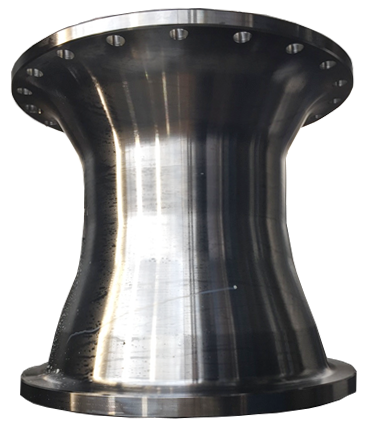
A subcontractor to the engineering industry was looking for a solution to apply back spot faces for the bolting that does the job without the time-consuming reclamping of the workpiece. The time used ...
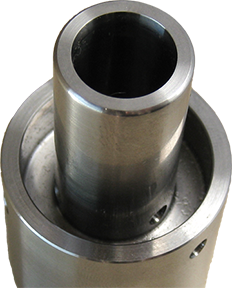
This aerospace manufacturer was looking for a solution for deburring three through-holes with four bore edges each for a fuel pump component on a rocket.
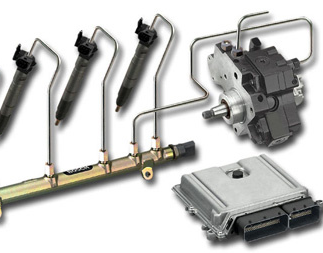
A precision machining supplier to the automotive industry who produces more than 1 million common rails per year was looking for a solution to automate the back deburring of a low pressure bore.
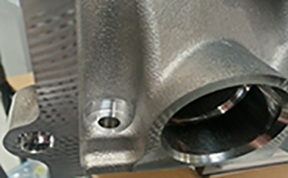
A manufacturer of motorsport engines was looking for a cost-effective solution for the application of counterbores.